Why do airplanes use an axial flow jet engine instead of a more compact centrifugal jet engine?Can an S-duct fit a turbofan exhaust instead of the intake?Why don't planes use pulsejets?Why were rotary vane compressors never used in jet engines?What does the actual path of air within a turbojet engine look like?How is bleed air used to start a jet engine?Where does turbine vane and blade cooling air come from?Is my understanding of subsonic inlets correct?Would a ducted fan with a nozzle like a jet engine have more thrust than a normal ducted fan?Are centrifugal turbojets easier to make than axial ones?Why don't modern jet engines use forced exhaust mixing?Why are liquid ring compressors not used in a jet engine?
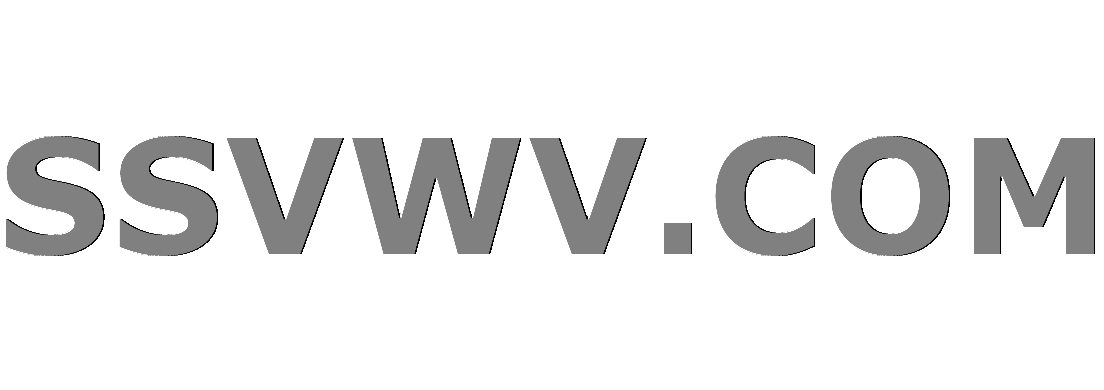
Multi tool use
Does Turkey make the "structural steel frame" for the F-35 fighter?
Minimum number of turns to capture all pieces in Checkers
What's the meaning of Electrical Inches?
When and why did the House rules change to permit an inquiry without a vote?
Examples of problems with non-convex constraint functions but convex feasible region
Do any languages mark social distinctions other than gender and status?
Meaning of “Bulldog drooled courses through his jowls”
Did I Traumatize My Puppy?
What actually is "unallocated space"?
How to figure out key from key signature?
Is it allowed to let the engine of an aircraft idle without a pilot in the plane. (For both helicopters and aeroplanes)
Who inspired the character Geordi La Forge?
Can I use Oko's ability targetting a creature with protection from green?
Why were germanium diodes so fast and germanium transistors so slow?
What plausible reasons why people forget they didn't originally live on this new planet?
Limit of sequence (by definiton)
Why is this a missed win?
Can elves trance in armor without any downsides?
Why did my relationship with my wife go down by two hearts?
Did it take 3 minutes to reload a musket when the second amendment to the US constitution was ratified?
How does an Evocation Wizard's Overchannel ability interact with Chaos Bolt?
How much does freezing grapes longer sweeten them more?
How can I seal 8 inch round holes in my siding?
Tear in RFs, not losing air
Why do airplanes use an axial flow jet engine instead of a more compact centrifugal jet engine?
Can an S-duct fit a turbofan exhaust instead of the intake?Why don't planes use pulsejets?Why were rotary vane compressors never used in jet engines?What does the actual path of air within a turbojet engine look like?How is bleed air used to start a jet engine?Where does turbine vane and blade cooling air come from?Is my understanding of subsonic inlets correct?Would a ducted fan with a nozzle like a jet engine have more thrust than a normal ducted fan?Are centrifugal turbojets easier to make than axial ones?Why don't modern jet engines use forced exhaust mixing?Why are liquid ring compressors not used in a jet engine?
.everyoneloves__top-leaderboard:empty,.everyoneloves__mid-leaderboard:empty,.everyoneloves__bot-mid-leaderboard:empty
margin-bottom:0;
$begingroup$
Axial flow jet engines take up a lot of space. Centrifugal jet engines create high pressure. Can you create a centrifugal air pump that pushes as much air as a axial jet engine. Centrifugal air engines reach higher speeds from my research. What are the main disadvantages of centrifugal air engines from the standard axial engines.
jet-engine engine-design compressor
$endgroup$
add a comment
|
$begingroup$
Axial flow jet engines take up a lot of space. Centrifugal jet engines create high pressure. Can you create a centrifugal air pump that pushes as much air as a axial jet engine. Centrifugal air engines reach higher speeds from my research. What are the main disadvantages of centrifugal air engines from the standard axial engines.
jet-engine engine-design compressor
$endgroup$
add a comment
|
$begingroup$
Axial flow jet engines take up a lot of space. Centrifugal jet engines create high pressure. Can you create a centrifugal air pump that pushes as much air as a axial jet engine. Centrifugal air engines reach higher speeds from my research. What are the main disadvantages of centrifugal air engines from the standard axial engines.
jet-engine engine-design compressor
$endgroup$
Axial flow jet engines take up a lot of space. Centrifugal jet engines create high pressure. Can you create a centrifugal air pump that pushes as much air as a axial jet engine. Centrifugal air engines reach higher speeds from my research. What are the main disadvantages of centrifugal air engines from the standard axial engines.
jet-engine engine-design compressor
jet-engine engine-design compressor
edited May 25 at 13:18


ymb1
81.7k9 gold badges271 silver badges444 bronze badges
81.7k9 gold badges271 silver badges444 bronze badges
asked May 24 at 21:12
UseruuuUseruuu
1061 silver badge4 bronze badges
1061 silver badge4 bronze badges
add a comment
|
add a comment
|
4 Answers
4
active
oldest
votes
$begingroup$
Centrifugal compressors only produce a more compact engine at low mass flow, which means low thrust.
The amount of thrust an engine can produce is proportional to its intake area times exhaust velocity. Increasing the latter is undesirable, as energy and thus fuel consumption is proportional to velocity squared. So engine designers target mass flow to gain more thrust.
Since they are 3D structures, in a naive solid design (that you'd find in early jets and microturbines), the mass of a centrifugal compressor grows in cubic proportion to its diameter, while frontal area, which limits its mass flow and thus its thrust, increases only as diameter squared. This creates a cube-square law.
Large real-life parts are filled with lightening and cooling channels, so the law is more complex, Still, the end result is that the mass of centrifugal compressors grows faster than power, and at the highest power levels they become prohibitively heavy even for fixed powerplant machinery, where durability otherwise trumps weight. With axial compressors, the flat design with short air flow path allows mass to only grow in direct proportion to power, and very powerful engines can be built within reasonable dimensions.
High-performance engines, such as those in commercial aircraft, also need to pack more thrust into the smallest cross-section they can, while maintaining efficiency, so as to reduce drag and also fit under the wings, enabling heavier jets. Axial compressors offer a lot more intake area for any given cross-section - thus more thrust.
The smallest jets, where thrust requirements are small and the engine's cross-section is very small compared to the fuselage, can afford the extra diameter of a centrifugal or diagonal flow compressor. Yes, it's the same cube-square law that keeps the engine cross-section to total cross-section ratio increasing as aircraft go up in size. Small centrifugal compressors are simpler, easier to build, and more robust than small axial ones.
So in every industry there is a crossover point from centrifugal to axial. For aircraft where drag is critical, it's just above small bizjets, mobile ground and helicopter turbines stay centrifugal or mixed up to a few MW, and in the tens of megawatts even fixed powerplants switch from axial/centrifugal to all-axial. Engines close to that crossover point typically combine axial and centrifugal stages, and newer diagonal compressors offer an even more tailored compromise.
$endgroup$
1
$begingroup$
Thank you, a very thorough yet easy to follow answer.
$endgroup$
– Mast
May 25 at 16:29
$begingroup$
"Centrifugal compressors are only more compact at low mass flow" no they aren't, they are more compact at any mass flow. A large part of the frontal area cannot be used for airflow, is the issue in larger engines.
$endgroup$
– Koyovis
May 26 at 2:31
$begingroup$
@Koyovis Define "compact" then. Inlets have to be sized for required airflow, so, for airliner engines that are only as wide as their inlets, a wider compressor will mean a wider and heavier engine. Centrifugal compressors are compact in smaller engines, but supersizing them doesn't maintain that - axials are better at ingesting as much air as possible in given engine size.
$endgroup$
– Therac
May 26 at 7:44
$begingroup$
"The necessary mass of a centrifugal compressor grows in cubic proportion to its diameter" Not necessarily: The length of an engine might even shrink when increasing the diameter. In this case the volume (and therefore the weight) would grow less than squared.
$endgroup$
– Martin Rosenau
May 26 at 15:37
$begingroup$
Mass of the centrifugal compressor grows exponentially compared to the mass of three axial stages? The centrifugal compressor can be hollowed out, the main stress bearing material is at the impeller tip.
$endgroup$
– Koyovis
Jun 11 at 1:43
|
show 3 more comments
$begingroup$
Axial turbine engines take up a lot of space...lengthwise. Centrifugal compressors are shorter and wider, and are very often used in turboprop and turboshaft engines, for instance the Rolls Royce Dart is a single axis turboprop engine. The photo demonstrates the compactness of the engine...lengthwise.
.
Can you create a centrifugal air pump that pushes as much air as a axial jet engine.
Yes you can. It will have two main issues:
- The losses in the centrifugal compressors will be higher than for an axial configuration reaching the same compression ratio.
- Part of the frontal area cannot be used for airflow.
What are the main disadvantages of centrifugal air engines from the standard axial engines.
Centrifugal compressors:
- Are slightly less efficient than axial compressors (for a given compression ratio).
- Expel the airflow perpendicular to free stream, so that if multiple stages are required the airflow must be guided into quite a bendy pathway, with additional negative impact on efficiency.
- Result in an engine with a larger frontal area.
Advantages are:
- Centrifugal compressors achieve higher compression ratios than axial compressors - per stage. Compression ratios of 4 - 6, while an axial stage can only do 1.4 - 1.6.
- They are of a more robust and often less costly construction.
Larger engines (high mass flow, high compression ratio and minimal frontal area) use axial compressors almost exclusively: the internal losses are lowest. Centrifugal compressors are used for design cases where other factors than efficiency are of interest, such as cost and limitation of length for helicopter turboshafts.
An example of the use of a centrifugal compressor in a turbofan engine is the Garrett AiResearch ATF3. A 3-shaft engine, with the fan on shaft 1, five axial stages on shaft 2, and a centrifugal stage on shaft 3.
Picture source
The hot exhaust stream is deflected back into the fan bypass, which cools it down and results in a low IR signature. This engine is used in the Dassault Falcon. Note that there is no principal technical difficulty to scale this engine up to A380 level, other than the decreased efficiency due to the multiple deflections in the airstream. The wider frontal area is not a problem in the compressor part, and the total compression ratio increases a lot using this final stage.
As in the ATF3, centrifugal compressors are often combined with an axial stage, which pre-whirls the air stream into the centrifugal compressor and increases both efficiency and max compression ratio per single stage, as compared to a flat single stage.
$endgroup$
add a comment
|
$begingroup$
While a centrifugal compressor can acheive greater compression than a single compressor stage in an axial flow engine, the axial flow design allows for multiple compressor stages, achieving higher overall compression of the air and consequently greater efficiency. Centrifugal flow jet engines are, however, tough and reliable.
$endgroup$
$begingroup$
Centrifugal compressors can also be multi-staged.
$endgroup$
– Koyovis
May 26 at 20:06
add a comment
|
$begingroup$
All existing centrifugal-compressor aircraft engines have been turbojets or turboprops.
Aside from their low power compared with modern turbofans (the Rolls-Royce Dart mentioned in another answer produced about 1 MW, compared with 50MW for a modern large turbofan engine core) the larger diameter of a centrifugal compressor would make it hard to design an efficient turbofan, by restricting the area of the fan duct.
Increasing the outer diameter of the fan blades to enlarge the bypass duct is not a practical option, since it is limited by the ground clearance of the aircraft. Trying to avoid that issue with very large diameter tail-mounted engines would just create a different set of design problems.
$endgroup$
1
$begingroup$
Not all; the Pratt & Whitney Canada PW600 is a turbofan (albeit a tiny one) with a centrifugal core compressor.
$endgroup$
– Sean
May 25 at 22:05
$begingroup$
The RR Dart powers a propeller. Talk about a large diameter fan...
$endgroup$
– Koyovis
May 26 at 1:17
add a comment
|
Your Answer
StackExchange.ready(function()
var channelOptions =
tags: "".split(" "),
id: "528"
;
initTagRenderer("".split(" "), "".split(" "), channelOptions);
StackExchange.using("externalEditor", function()
// Have to fire editor after snippets, if snippets enabled
if (StackExchange.settings.snippets.snippetsEnabled)
StackExchange.using("snippets", function()
createEditor();
);
else
createEditor();
);
function createEditor()
StackExchange.prepareEditor(
heartbeatType: 'answer',
autoActivateHeartbeat: false,
convertImagesToLinks: false,
noModals: true,
showLowRepImageUploadWarning: true,
reputationToPostImages: null,
bindNavPrevention: true,
postfix: "",
imageUploader:
brandingHtml: "Powered by u003ca class="icon-imgur-white" href="https://imgur.com/"u003eu003c/au003e",
contentPolicyHtml: "User contributions licensed under u003ca href="https://creativecommons.org/licenses/by-sa/4.0/"u003ecc by-sa 4.0 with attribution requiredu003c/au003e u003ca href="https://stackoverflow.com/legal/content-policy"u003e(content policy)u003c/au003e",
allowUrls: true
,
noCode: true, onDemand: true,
discardSelector: ".discard-answer"
,immediatelyShowMarkdownHelp:true
);
);
Sign up or log in
StackExchange.ready(function ()
StackExchange.helpers.onClickDraftSave('#login-link');
);
Sign up using Google
Sign up using Facebook
Sign up using Email and Password
Post as a guest
Required, but never shown
StackExchange.ready(
function ()
StackExchange.openid.initPostLogin('.new-post-login', 'https%3a%2f%2faviation.stackexchange.com%2fquestions%2f64717%2fwhy-do-airplanes-use-an-axial-flow-jet-engine-instead-of-a-more-compact-centrifu%23new-answer', 'question_page');
);
Post as a guest
Required, but never shown
4 Answers
4
active
oldest
votes
4 Answers
4
active
oldest
votes
active
oldest
votes
active
oldest
votes
$begingroup$
Centrifugal compressors only produce a more compact engine at low mass flow, which means low thrust.
The amount of thrust an engine can produce is proportional to its intake area times exhaust velocity. Increasing the latter is undesirable, as energy and thus fuel consumption is proportional to velocity squared. So engine designers target mass flow to gain more thrust.
Since they are 3D structures, in a naive solid design (that you'd find in early jets and microturbines), the mass of a centrifugal compressor grows in cubic proportion to its diameter, while frontal area, which limits its mass flow and thus its thrust, increases only as diameter squared. This creates a cube-square law.
Large real-life parts are filled with lightening and cooling channels, so the law is more complex, Still, the end result is that the mass of centrifugal compressors grows faster than power, and at the highest power levels they become prohibitively heavy even for fixed powerplant machinery, where durability otherwise trumps weight. With axial compressors, the flat design with short air flow path allows mass to only grow in direct proportion to power, and very powerful engines can be built within reasonable dimensions.
High-performance engines, such as those in commercial aircraft, also need to pack more thrust into the smallest cross-section they can, while maintaining efficiency, so as to reduce drag and also fit under the wings, enabling heavier jets. Axial compressors offer a lot more intake area for any given cross-section - thus more thrust.
The smallest jets, where thrust requirements are small and the engine's cross-section is very small compared to the fuselage, can afford the extra diameter of a centrifugal or diagonal flow compressor. Yes, it's the same cube-square law that keeps the engine cross-section to total cross-section ratio increasing as aircraft go up in size. Small centrifugal compressors are simpler, easier to build, and more robust than small axial ones.
So in every industry there is a crossover point from centrifugal to axial. For aircraft where drag is critical, it's just above small bizjets, mobile ground and helicopter turbines stay centrifugal or mixed up to a few MW, and in the tens of megawatts even fixed powerplants switch from axial/centrifugal to all-axial. Engines close to that crossover point typically combine axial and centrifugal stages, and newer diagonal compressors offer an even more tailored compromise.
$endgroup$
1
$begingroup$
Thank you, a very thorough yet easy to follow answer.
$endgroup$
– Mast
May 25 at 16:29
$begingroup$
"Centrifugal compressors are only more compact at low mass flow" no they aren't, they are more compact at any mass flow. A large part of the frontal area cannot be used for airflow, is the issue in larger engines.
$endgroup$
– Koyovis
May 26 at 2:31
$begingroup$
@Koyovis Define "compact" then. Inlets have to be sized for required airflow, so, for airliner engines that are only as wide as their inlets, a wider compressor will mean a wider and heavier engine. Centrifugal compressors are compact in smaller engines, but supersizing them doesn't maintain that - axials are better at ingesting as much air as possible in given engine size.
$endgroup$
– Therac
May 26 at 7:44
$begingroup$
"The necessary mass of a centrifugal compressor grows in cubic proportion to its diameter" Not necessarily: The length of an engine might even shrink when increasing the diameter. In this case the volume (and therefore the weight) would grow less than squared.
$endgroup$
– Martin Rosenau
May 26 at 15:37
$begingroup$
Mass of the centrifugal compressor grows exponentially compared to the mass of three axial stages? The centrifugal compressor can be hollowed out, the main stress bearing material is at the impeller tip.
$endgroup$
– Koyovis
Jun 11 at 1:43
|
show 3 more comments
$begingroup$
Centrifugal compressors only produce a more compact engine at low mass flow, which means low thrust.
The amount of thrust an engine can produce is proportional to its intake area times exhaust velocity. Increasing the latter is undesirable, as energy and thus fuel consumption is proportional to velocity squared. So engine designers target mass flow to gain more thrust.
Since they are 3D structures, in a naive solid design (that you'd find in early jets and microturbines), the mass of a centrifugal compressor grows in cubic proportion to its diameter, while frontal area, which limits its mass flow and thus its thrust, increases only as diameter squared. This creates a cube-square law.
Large real-life parts are filled with lightening and cooling channels, so the law is more complex, Still, the end result is that the mass of centrifugal compressors grows faster than power, and at the highest power levels they become prohibitively heavy even for fixed powerplant machinery, where durability otherwise trumps weight. With axial compressors, the flat design with short air flow path allows mass to only grow in direct proportion to power, and very powerful engines can be built within reasonable dimensions.
High-performance engines, such as those in commercial aircraft, also need to pack more thrust into the smallest cross-section they can, while maintaining efficiency, so as to reduce drag and also fit under the wings, enabling heavier jets. Axial compressors offer a lot more intake area for any given cross-section - thus more thrust.
The smallest jets, where thrust requirements are small and the engine's cross-section is very small compared to the fuselage, can afford the extra diameter of a centrifugal or diagonal flow compressor. Yes, it's the same cube-square law that keeps the engine cross-section to total cross-section ratio increasing as aircraft go up in size. Small centrifugal compressors are simpler, easier to build, and more robust than small axial ones.
So in every industry there is a crossover point from centrifugal to axial. For aircraft where drag is critical, it's just above small bizjets, mobile ground and helicopter turbines stay centrifugal or mixed up to a few MW, and in the tens of megawatts even fixed powerplants switch from axial/centrifugal to all-axial. Engines close to that crossover point typically combine axial and centrifugal stages, and newer diagonal compressors offer an even more tailored compromise.
$endgroup$
1
$begingroup$
Thank you, a very thorough yet easy to follow answer.
$endgroup$
– Mast
May 25 at 16:29
$begingroup$
"Centrifugal compressors are only more compact at low mass flow" no they aren't, they are more compact at any mass flow. A large part of the frontal area cannot be used for airflow, is the issue in larger engines.
$endgroup$
– Koyovis
May 26 at 2:31
$begingroup$
@Koyovis Define "compact" then. Inlets have to be sized for required airflow, so, for airliner engines that are only as wide as their inlets, a wider compressor will mean a wider and heavier engine. Centrifugal compressors are compact in smaller engines, but supersizing them doesn't maintain that - axials are better at ingesting as much air as possible in given engine size.
$endgroup$
– Therac
May 26 at 7:44
$begingroup$
"The necessary mass of a centrifugal compressor grows in cubic proportion to its diameter" Not necessarily: The length of an engine might even shrink when increasing the diameter. In this case the volume (and therefore the weight) would grow less than squared.
$endgroup$
– Martin Rosenau
May 26 at 15:37
$begingroup$
Mass of the centrifugal compressor grows exponentially compared to the mass of three axial stages? The centrifugal compressor can be hollowed out, the main stress bearing material is at the impeller tip.
$endgroup$
– Koyovis
Jun 11 at 1:43
|
show 3 more comments
$begingroup$
Centrifugal compressors only produce a more compact engine at low mass flow, which means low thrust.
The amount of thrust an engine can produce is proportional to its intake area times exhaust velocity. Increasing the latter is undesirable, as energy and thus fuel consumption is proportional to velocity squared. So engine designers target mass flow to gain more thrust.
Since they are 3D structures, in a naive solid design (that you'd find in early jets and microturbines), the mass of a centrifugal compressor grows in cubic proportion to its diameter, while frontal area, which limits its mass flow and thus its thrust, increases only as diameter squared. This creates a cube-square law.
Large real-life parts are filled with lightening and cooling channels, so the law is more complex, Still, the end result is that the mass of centrifugal compressors grows faster than power, and at the highest power levels they become prohibitively heavy even for fixed powerplant machinery, where durability otherwise trumps weight. With axial compressors, the flat design with short air flow path allows mass to only grow in direct proportion to power, and very powerful engines can be built within reasonable dimensions.
High-performance engines, such as those in commercial aircraft, also need to pack more thrust into the smallest cross-section they can, while maintaining efficiency, so as to reduce drag and also fit under the wings, enabling heavier jets. Axial compressors offer a lot more intake area for any given cross-section - thus more thrust.
The smallest jets, where thrust requirements are small and the engine's cross-section is very small compared to the fuselage, can afford the extra diameter of a centrifugal or diagonal flow compressor. Yes, it's the same cube-square law that keeps the engine cross-section to total cross-section ratio increasing as aircraft go up in size. Small centrifugal compressors are simpler, easier to build, and more robust than small axial ones.
So in every industry there is a crossover point from centrifugal to axial. For aircraft where drag is critical, it's just above small bizjets, mobile ground and helicopter turbines stay centrifugal or mixed up to a few MW, and in the tens of megawatts even fixed powerplants switch from axial/centrifugal to all-axial. Engines close to that crossover point typically combine axial and centrifugal stages, and newer diagonal compressors offer an even more tailored compromise.
$endgroup$
Centrifugal compressors only produce a more compact engine at low mass flow, which means low thrust.
The amount of thrust an engine can produce is proportional to its intake area times exhaust velocity. Increasing the latter is undesirable, as energy and thus fuel consumption is proportional to velocity squared. So engine designers target mass flow to gain more thrust.
Since they are 3D structures, in a naive solid design (that you'd find in early jets and microturbines), the mass of a centrifugal compressor grows in cubic proportion to its diameter, while frontal area, which limits its mass flow and thus its thrust, increases only as diameter squared. This creates a cube-square law.
Large real-life parts are filled with lightening and cooling channels, so the law is more complex, Still, the end result is that the mass of centrifugal compressors grows faster than power, and at the highest power levels they become prohibitively heavy even for fixed powerplant machinery, where durability otherwise trumps weight. With axial compressors, the flat design with short air flow path allows mass to only grow in direct proportion to power, and very powerful engines can be built within reasonable dimensions.
High-performance engines, such as those in commercial aircraft, also need to pack more thrust into the smallest cross-section they can, while maintaining efficiency, so as to reduce drag and also fit under the wings, enabling heavier jets. Axial compressors offer a lot more intake area for any given cross-section - thus more thrust.
The smallest jets, where thrust requirements are small and the engine's cross-section is very small compared to the fuselage, can afford the extra diameter of a centrifugal or diagonal flow compressor. Yes, it's the same cube-square law that keeps the engine cross-section to total cross-section ratio increasing as aircraft go up in size. Small centrifugal compressors are simpler, easier to build, and more robust than small axial ones.
So in every industry there is a crossover point from centrifugal to axial. For aircraft where drag is critical, it's just above small bizjets, mobile ground and helicopter turbines stay centrifugal or mixed up to a few MW, and in the tens of megawatts even fixed powerplants switch from axial/centrifugal to all-axial. Engines close to that crossover point typically combine axial and centrifugal stages, and newer diagonal compressors offer an even more tailored compromise.
edited Jun 12 at 8:01
answered May 25 at 8:24
TheracTherac
10.9k1 gold badge33 silver badges50 bronze badges
10.9k1 gold badge33 silver badges50 bronze badges
1
$begingroup$
Thank you, a very thorough yet easy to follow answer.
$endgroup$
– Mast
May 25 at 16:29
$begingroup$
"Centrifugal compressors are only more compact at low mass flow" no they aren't, they are more compact at any mass flow. A large part of the frontal area cannot be used for airflow, is the issue in larger engines.
$endgroup$
– Koyovis
May 26 at 2:31
$begingroup$
@Koyovis Define "compact" then. Inlets have to be sized for required airflow, so, for airliner engines that are only as wide as their inlets, a wider compressor will mean a wider and heavier engine. Centrifugal compressors are compact in smaller engines, but supersizing them doesn't maintain that - axials are better at ingesting as much air as possible in given engine size.
$endgroup$
– Therac
May 26 at 7:44
$begingroup$
"The necessary mass of a centrifugal compressor grows in cubic proportion to its diameter" Not necessarily: The length of an engine might even shrink when increasing the diameter. In this case the volume (and therefore the weight) would grow less than squared.
$endgroup$
– Martin Rosenau
May 26 at 15:37
$begingroup$
Mass of the centrifugal compressor grows exponentially compared to the mass of three axial stages? The centrifugal compressor can be hollowed out, the main stress bearing material is at the impeller tip.
$endgroup$
– Koyovis
Jun 11 at 1:43
|
show 3 more comments
1
$begingroup$
Thank you, a very thorough yet easy to follow answer.
$endgroup$
– Mast
May 25 at 16:29
$begingroup$
"Centrifugal compressors are only more compact at low mass flow" no they aren't, they are more compact at any mass flow. A large part of the frontal area cannot be used for airflow, is the issue in larger engines.
$endgroup$
– Koyovis
May 26 at 2:31
$begingroup$
@Koyovis Define "compact" then. Inlets have to be sized for required airflow, so, for airliner engines that are only as wide as their inlets, a wider compressor will mean a wider and heavier engine. Centrifugal compressors are compact in smaller engines, but supersizing them doesn't maintain that - axials are better at ingesting as much air as possible in given engine size.
$endgroup$
– Therac
May 26 at 7:44
$begingroup$
"The necessary mass of a centrifugal compressor grows in cubic proportion to its diameter" Not necessarily: The length of an engine might even shrink when increasing the diameter. In this case the volume (and therefore the weight) would grow less than squared.
$endgroup$
– Martin Rosenau
May 26 at 15:37
$begingroup$
Mass of the centrifugal compressor grows exponentially compared to the mass of three axial stages? The centrifugal compressor can be hollowed out, the main stress bearing material is at the impeller tip.
$endgroup$
– Koyovis
Jun 11 at 1:43
1
1
$begingroup$
Thank you, a very thorough yet easy to follow answer.
$endgroup$
– Mast
May 25 at 16:29
$begingroup$
Thank you, a very thorough yet easy to follow answer.
$endgroup$
– Mast
May 25 at 16:29
$begingroup$
"Centrifugal compressors are only more compact at low mass flow" no they aren't, they are more compact at any mass flow. A large part of the frontal area cannot be used for airflow, is the issue in larger engines.
$endgroup$
– Koyovis
May 26 at 2:31
$begingroup$
"Centrifugal compressors are only more compact at low mass flow" no they aren't, they are more compact at any mass flow. A large part of the frontal area cannot be used for airflow, is the issue in larger engines.
$endgroup$
– Koyovis
May 26 at 2:31
$begingroup$
@Koyovis Define "compact" then. Inlets have to be sized for required airflow, so, for airliner engines that are only as wide as their inlets, a wider compressor will mean a wider and heavier engine. Centrifugal compressors are compact in smaller engines, but supersizing them doesn't maintain that - axials are better at ingesting as much air as possible in given engine size.
$endgroup$
– Therac
May 26 at 7:44
$begingroup$
@Koyovis Define "compact" then. Inlets have to be sized for required airflow, so, for airliner engines that are only as wide as their inlets, a wider compressor will mean a wider and heavier engine. Centrifugal compressors are compact in smaller engines, but supersizing them doesn't maintain that - axials are better at ingesting as much air as possible in given engine size.
$endgroup$
– Therac
May 26 at 7:44
$begingroup$
"The necessary mass of a centrifugal compressor grows in cubic proportion to its diameter" Not necessarily: The length of an engine might even shrink when increasing the diameter. In this case the volume (and therefore the weight) would grow less than squared.
$endgroup$
– Martin Rosenau
May 26 at 15:37
$begingroup$
"The necessary mass of a centrifugal compressor grows in cubic proportion to its diameter" Not necessarily: The length of an engine might even shrink when increasing the diameter. In this case the volume (and therefore the weight) would grow less than squared.
$endgroup$
– Martin Rosenau
May 26 at 15:37
$begingroup$
Mass of the centrifugal compressor grows exponentially compared to the mass of three axial stages? The centrifugal compressor can be hollowed out, the main stress bearing material is at the impeller tip.
$endgroup$
– Koyovis
Jun 11 at 1:43
$begingroup$
Mass of the centrifugal compressor grows exponentially compared to the mass of three axial stages? The centrifugal compressor can be hollowed out, the main stress bearing material is at the impeller tip.
$endgroup$
– Koyovis
Jun 11 at 1:43
|
show 3 more comments
$begingroup$
Axial turbine engines take up a lot of space...lengthwise. Centrifugal compressors are shorter and wider, and are very often used in turboprop and turboshaft engines, for instance the Rolls Royce Dart is a single axis turboprop engine. The photo demonstrates the compactness of the engine...lengthwise.
.
Can you create a centrifugal air pump that pushes as much air as a axial jet engine.
Yes you can. It will have two main issues:
- The losses in the centrifugal compressors will be higher than for an axial configuration reaching the same compression ratio.
- Part of the frontal area cannot be used for airflow.
What are the main disadvantages of centrifugal air engines from the standard axial engines.
Centrifugal compressors:
- Are slightly less efficient than axial compressors (for a given compression ratio).
- Expel the airflow perpendicular to free stream, so that if multiple stages are required the airflow must be guided into quite a bendy pathway, with additional negative impact on efficiency.
- Result in an engine with a larger frontal area.
Advantages are:
- Centrifugal compressors achieve higher compression ratios than axial compressors - per stage. Compression ratios of 4 - 6, while an axial stage can only do 1.4 - 1.6.
- They are of a more robust and often less costly construction.
Larger engines (high mass flow, high compression ratio and minimal frontal area) use axial compressors almost exclusively: the internal losses are lowest. Centrifugal compressors are used for design cases where other factors than efficiency are of interest, such as cost and limitation of length for helicopter turboshafts.
An example of the use of a centrifugal compressor in a turbofan engine is the Garrett AiResearch ATF3. A 3-shaft engine, with the fan on shaft 1, five axial stages on shaft 2, and a centrifugal stage on shaft 3.
Picture source
The hot exhaust stream is deflected back into the fan bypass, which cools it down and results in a low IR signature. This engine is used in the Dassault Falcon. Note that there is no principal technical difficulty to scale this engine up to A380 level, other than the decreased efficiency due to the multiple deflections in the airstream. The wider frontal area is not a problem in the compressor part, and the total compression ratio increases a lot using this final stage.
As in the ATF3, centrifugal compressors are often combined with an axial stage, which pre-whirls the air stream into the centrifugal compressor and increases both efficiency and max compression ratio per single stage, as compared to a flat single stage.
$endgroup$
add a comment
|
$begingroup$
Axial turbine engines take up a lot of space...lengthwise. Centrifugal compressors are shorter and wider, and are very often used in turboprop and turboshaft engines, for instance the Rolls Royce Dart is a single axis turboprop engine. The photo demonstrates the compactness of the engine...lengthwise.
.
Can you create a centrifugal air pump that pushes as much air as a axial jet engine.
Yes you can. It will have two main issues:
- The losses in the centrifugal compressors will be higher than for an axial configuration reaching the same compression ratio.
- Part of the frontal area cannot be used for airflow.
What are the main disadvantages of centrifugal air engines from the standard axial engines.
Centrifugal compressors:
- Are slightly less efficient than axial compressors (for a given compression ratio).
- Expel the airflow perpendicular to free stream, so that if multiple stages are required the airflow must be guided into quite a bendy pathway, with additional negative impact on efficiency.
- Result in an engine with a larger frontal area.
Advantages are:
- Centrifugal compressors achieve higher compression ratios than axial compressors - per stage. Compression ratios of 4 - 6, while an axial stage can only do 1.4 - 1.6.
- They are of a more robust and often less costly construction.
Larger engines (high mass flow, high compression ratio and minimal frontal area) use axial compressors almost exclusively: the internal losses are lowest. Centrifugal compressors are used for design cases where other factors than efficiency are of interest, such as cost and limitation of length for helicopter turboshafts.
An example of the use of a centrifugal compressor in a turbofan engine is the Garrett AiResearch ATF3. A 3-shaft engine, with the fan on shaft 1, five axial stages on shaft 2, and a centrifugal stage on shaft 3.
Picture source
The hot exhaust stream is deflected back into the fan bypass, which cools it down and results in a low IR signature. This engine is used in the Dassault Falcon. Note that there is no principal technical difficulty to scale this engine up to A380 level, other than the decreased efficiency due to the multiple deflections in the airstream. The wider frontal area is not a problem in the compressor part, and the total compression ratio increases a lot using this final stage.
As in the ATF3, centrifugal compressors are often combined with an axial stage, which pre-whirls the air stream into the centrifugal compressor and increases both efficiency and max compression ratio per single stage, as compared to a flat single stage.
$endgroup$
add a comment
|
$begingroup$
Axial turbine engines take up a lot of space...lengthwise. Centrifugal compressors are shorter and wider, and are very often used in turboprop and turboshaft engines, for instance the Rolls Royce Dart is a single axis turboprop engine. The photo demonstrates the compactness of the engine...lengthwise.
.
Can you create a centrifugal air pump that pushes as much air as a axial jet engine.
Yes you can. It will have two main issues:
- The losses in the centrifugal compressors will be higher than for an axial configuration reaching the same compression ratio.
- Part of the frontal area cannot be used for airflow.
What are the main disadvantages of centrifugal air engines from the standard axial engines.
Centrifugal compressors:
- Are slightly less efficient than axial compressors (for a given compression ratio).
- Expel the airflow perpendicular to free stream, so that if multiple stages are required the airflow must be guided into quite a bendy pathway, with additional negative impact on efficiency.
- Result in an engine with a larger frontal area.
Advantages are:
- Centrifugal compressors achieve higher compression ratios than axial compressors - per stage. Compression ratios of 4 - 6, while an axial stage can only do 1.4 - 1.6.
- They are of a more robust and often less costly construction.
Larger engines (high mass flow, high compression ratio and minimal frontal area) use axial compressors almost exclusively: the internal losses are lowest. Centrifugal compressors are used for design cases where other factors than efficiency are of interest, such as cost and limitation of length for helicopter turboshafts.
An example of the use of a centrifugal compressor in a turbofan engine is the Garrett AiResearch ATF3. A 3-shaft engine, with the fan on shaft 1, five axial stages on shaft 2, and a centrifugal stage on shaft 3.
Picture source
The hot exhaust stream is deflected back into the fan bypass, which cools it down and results in a low IR signature. This engine is used in the Dassault Falcon. Note that there is no principal technical difficulty to scale this engine up to A380 level, other than the decreased efficiency due to the multiple deflections in the airstream. The wider frontal area is not a problem in the compressor part, and the total compression ratio increases a lot using this final stage.
As in the ATF3, centrifugal compressors are often combined with an axial stage, which pre-whirls the air stream into the centrifugal compressor and increases both efficiency and max compression ratio per single stage, as compared to a flat single stage.
$endgroup$
Axial turbine engines take up a lot of space...lengthwise. Centrifugal compressors are shorter and wider, and are very often used in turboprop and turboshaft engines, for instance the Rolls Royce Dart is a single axis turboprop engine. The photo demonstrates the compactness of the engine...lengthwise.
.
Can you create a centrifugal air pump that pushes as much air as a axial jet engine.
Yes you can. It will have two main issues:
- The losses in the centrifugal compressors will be higher than for an axial configuration reaching the same compression ratio.
- Part of the frontal area cannot be used for airflow.
What are the main disadvantages of centrifugal air engines from the standard axial engines.
Centrifugal compressors:
- Are slightly less efficient than axial compressors (for a given compression ratio).
- Expel the airflow perpendicular to free stream, so that if multiple stages are required the airflow must be guided into quite a bendy pathway, with additional negative impact on efficiency.
- Result in an engine with a larger frontal area.
Advantages are:
- Centrifugal compressors achieve higher compression ratios than axial compressors - per stage. Compression ratios of 4 - 6, while an axial stage can only do 1.4 - 1.6.
- They are of a more robust and often less costly construction.
Larger engines (high mass flow, high compression ratio and minimal frontal area) use axial compressors almost exclusively: the internal losses are lowest. Centrifugal compressors are used for design cases where other factors than efficiency are of interest, such as cost and limitation of length for helicopter turboshafts.
An example of the use of a centrifugal compressor in a turbofan engine is the Garrett AiResearch ATF3. A 3-shaft engine, with the fan on shaft 1, five axial stages on shaft 2, and a centrifugal stage on shaft 3.
Picture source
The hot exhaust stream is deflected back into the fan bypass, which cools it down and results in a low IR signature. This engine is used in the Dassault Falcon. Note that there is no principal technical difficulty to scale this engine up to A380 level, other than the decreased efficiency due to the multiple deflections in the airstream. The wider frontal area is not a problem in the compressor part, and the total compression ratio increases a lot using this final stage.
As in the ATF3, centrifugal compressors are often combined with an axial stage, which pre-whirls the air stream into the centrifugal compressor and increases both efficiency and max compression ratio per single stage, as compared to a flat single stage.
edited May 26 at 3:05
answered May 25 at 2:03
KoyovisKoyovis
38.3k9 gold badges104 silver badges198 bronze badges
38.3k9 gold badges104 silver badges198 bronze badges
add a comment
|
add a comment
|
$begingroup$
While a centrifugal compressor can acheive greater compression than a single compressor stage in an axial flow engine, the axial flow design allows for multiple compressor stages, achieving higher overall compression of the air and consequently greater efficiency. Centrifugal flow jet engines are, however, tough and reliable.
$endgroup$
$begingroup$
Centrifugal compressors can also be multi-staged.
$endgroup$
– Koyovis
May 26 at 20:06
add a comment
|
$begingroup$
While a centrifugal compressor can acheive greater compression than a single compressor stage in an axial flow engine, the axial flow design allows for multiple compressor stages, achieving higher overall compression of the air and consequently greater efficiency. Centrifugal flow jet engines are, however, tough and reliable.
$endgroup$
$begingroup$
Centrifugal compressors can also be multi-staged.
$endgroup$
– Koyovis
May 26 at 20:06
add a comment
|
$begingroup$
While a centrifugal compressor can acheive greater compression than a single compressor stage in an axial flow engine, the axial flow design allows for multiple compressor stages, achieving higher overall compression of the air and consequently greater efficiency. Centrifugal flow jet engines are, however, tough and reliable.
$endgroup$
While a centrifugal compressor can acheive greater compression than a single compressor stage in an axial flow engine, the axial flow design allows for multiple compressor stages, achieving higher overall compression of the air and consequently greater efficiency. Centrifugal flow jet engines are, however, tough and reliable.
answered May 25 at 11:17
J. SouthworthJ. Southworth
9902 silver badges6 bronze badges
9902 silver badges6 bronze badges
$begingroup$
Centrifugal compressors can also be multi-staged.
$endgroup$
– Koyovis
May 26 at 20:06
add a comment
|
$begingroup$
Centrifugal compressors can also be multi-staged.
$endgroup$
– Koyovis
May 26 at 20:06
$begingroup$
Centrifugal compressors can also be multi-staged.
$endgroup$
– Koyovis
May 26 at 20:06
$begingroup$
Centrifugal compressors can also be multi-staged.
$endgroup$
– Koyovis
May 26 at 20:06
add a comment
|
$begingroup$
All existing centrifugal-compressor aircraft engines have been turbojets or turboprops.
Aside from their low power compared with modern turbofans (the Rolls-Royce Dart mentioned in another answer produced about 1 MW, compared with 50MW for a modern large turbofan engine core) the larger diameter of a centrifugal compressor would make it hard to design an efficient turbofan, by restricting the area of the fan duct.
Increasing the outer diameter of the fan blades to enlarge the bypass duct is not a practical option, since it is limited by the ground clearance of the aircraft. Trying to avoid that issue with very large diameter tail-mounted engines would just create a different set of design problems.
$endgroup$
1
$begingroup$
Not all; the Pratt & Whitney Canada PW600 is a turbofan (albeit a tiny one) with a centrifugal core compressor.
$endgroup$
– Sean
May 25 at 22:05
$begingroup$
The RR Dart powers a propeller. Talk about a large diameter fan...
$endgroup$
– Koyovis
May 26 at 1:17
add a comment
|
$begingroup$
All existing centrifugal-compressor aircraft engines have been turbojets or turboprops.
Aside from their low power compared with modern turbofans (the Rolls-Royce Dart mentioned in another answer produced about 1 MW, compared with 50MW for a modern large turbofan engine core) the larger diameter of a centrifugal compressor would make it hard to design an efficient turbofan, by restricting the area of the fan duct.
Increasing the outer diameter of the fan blades to enlarge the bypass duct is not a practical option, since it is limited by the ground clearance of the aircraft. Trying to avoid that issue with very large diameter tail-mounted engines would just create a different set of design problems.
$endgroup$
1
$begingroup$
Not all; the Pratt & Whitney Canada PW600 is a turbofan (albeit a tiny one) with a centrifugal core compressor.
$endgroup$
– Sean
May 25 at 22:05
$begingroup$
The RR Dart powers a propeller. Talk about a large diameter fan...
$endgroup$
– Koyovis
May 26 at 1:17
add a comment
|
$begingroup$
All existing centrifugal-compressor aircraft engines have been turbojets or turboprops.
Aside from their low power compared with modern turbofans (the Rolls-Royce Dart mentioned in another answer produced about 1 MW, compared with 50MW for a modern large turbofan engine core) the larger diameter of a centrifugal compressor would make it hard to design an efficient turbofan, by restricting the area of the fan duct.
Increasing the outer diameter of the fan blades to enlarge the bypass duct is not a practical option, since it is limited by the ground clearance of the aircraft. Trying to avoid that issue with very large diameter tail-mounted engines would just create a different set of design problems.
$endgroup$
All existing centrifugal-compressor aircraft engines have been turbojets or turboprops.
Aside from their low power compared with modern turbofans (the Rolls-Royce Dart mentioned in another answer produced about 1 MW, compared with 50MW for a modern large turbofan engine core) the larger diameter of a centrifugal compressor would make it hard to design an efficient turbofan, by restricting the area of the fan duct.
Increasing the outer diameter of the fan blades to enlarge the bypass duct is not a practical option, since it is limited by the ground clearance of the aircraft. Trying to avoid that issue with very large diameter tail-mounted engines would just create a different set of design problems.
answered May 25 at 22:02
alephzeroalephzero
2,1566 silver badges15 bronze badges
2,1566 silver badges15 bronze badges
1
$begingroup$
Not all; the Pratt & Whitney Canada PW600 is a turbofan (albeit a tiny one) with a centrifugal core compressor.
$endgroup$
– Sean
May 25 at 22:05
$begingroup$
The RR Dart powers a propeller. Talk about a large diameter fan...
$endgroup$
– Koyovis
May 26 at 1:17
add a comment
|
1
$begingroup$
Not all; the Pratt & Whitney Canada PW600 is a turbofan (albeit a tiny one) with a centrifugal core compressor.
$endgroup$
– Sean
May 25 at 22:05
$begingroup$
The RR Dart powers a propeller. Talk about a large diameter fan...
$endgroup$
– Koyovis
May 26 at 1:17
1
1
$begingroup$
Not all; the Pratt & Whitney Canada PW600 is a turbofan (albeit a tiny one) with a centrifugal core compressor.
$endgroup$
– Sean
May 25 at 22:05
$begingroup$
Not all; the Pratt & Whitney Canada PW600 is a turbofan (albeit a tiny one) with a centrifugal core compressor.
$endgroup$
– Sean
May 25 at 22:05
$begingroup$
The RR Dart powers a propeller. Talk about a large diameter fan...
$endgroup$
– Koyovis
May 26 at 1:17
$begingroup$
The RR Dart powers a propeller. Talk about a large diameter fan...
$endgroup$
– Koyovis
May 26 at 1:17
add a comment
|
Thanks for contributing an answer to Aviation Stack Exchange!
- Please be sure to answer the question. Provide details and share your research!
But avoid …
- Asking for help, clarification, or responding to other answers.
- Making statements based on opinion; back them up with references or personal experience.
Use MathJax to format equations. MathJax reference.
To learn more, see our tips on writing great answers.
Sign up or log in
StackExchange.ready(function ()
StackExchange.helpers.onClickDraftSave('#login-link');
);
Sign up using Google
Sign up using Facebook
Sign up using Email and Password
Post as a guest
Required, but never shown
StackExchange.ready(
function ()
StackExchange.openid.initPostLogin('.new-post-login', 'https%3a%2f%2faviation.stackexchange.com%2fquestions%2f64717%2fwhy-do-airplanes-use-an-axial-flow-jet-engine-instead-of-a-more-compact-centrifu%23new-answer', 'question_page');
);
Post as a guest
Required, but never shown
Sign up or log in
StackExchange.ready(function ()
StackExchange.helpers.onClickDraftSave('#login-link');
);
Sign up using Google
Sign up using Facebook
Sign up using Email and Password
Post as a guest
Required, but never shown
Sign up or log in
StackExchange.ready(function ()
StackExchange.helpers.onClickDraftSave('#login-link');
);
Sign up using Google
Sign up using Facebook
Sign up using Email and Password
Post as a guest
Required, but never shown
Sign up or log in
StackExchange.ready(function ()
StackExchange.helpers.onClickDraftSave('#login-link');
);
Sign up using Google
Sign up using Facebook
Sign up using Email and Password
Sign up using Google
Sign up using Facebook
Sign up using Email and Password
Post as a guest
Required, but never shown
Required, but never shown
Required, but never shown
Required, but never shown
Required, but never shown
Required, but never shown
Required, but never shown
Required, but never shown
Required, but never shown
Meq6dzI,GaDwt,T oYNlb2GTaXhox8 a8J1GXkezIDRjAP80L