Why complex landing gears are used instead of simple, reliable and light weight muscle wire or shape memory alloys?Why are military and civil aircraft landing gear generally so different?Is it feasible to replace brakes on airplanes with electric motor/generator?Why are there so many moving parts used in the landing gear?Why are landing-distance and rejected-takeoff certification tests performed without thrust reversers?Why, and how, are barometric altimeters accurate enough for approach and landing?Why are the spoilers used as the backup controls instead of ailerons on the Boeing 777?
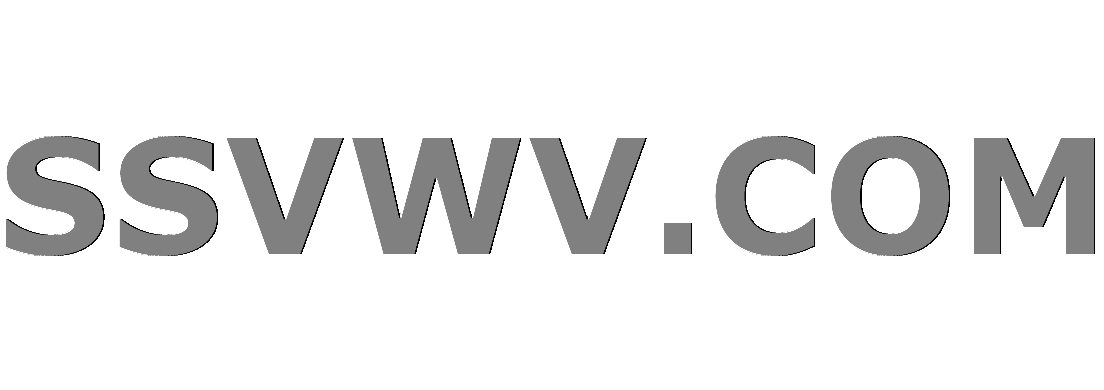
Multi tool use
Transferring 9 pegs on a 9x9 grid
I didn't do any exit passport control when leaving Japan. What should I do?
How to use an equalizer?
Is it realistic that an advanced species isn't good at war?
Is self-defense mutually exclusive of murder?
An employee has low self-confidence, and is performing poorly. How can I help?
What are the consequences for downstream actors of redistributing a work under a wider CC license than the copyright holder authorized?
What is the meaning of "shop-wise" in "… and talk turned shop-wise"?
Sanitise a high score table to remove offensive terms / usernames
Can you use the Wish spell to duplicate a 9th-level spell?
UK PM is taking his proposal to EU but has not proposed to his own parliament - can he legally bypass the UK parliament?
what to upgrade first
Why did the range based for loop specification change in C++17
How to remind myself to lock my doors
What are the different ways one can refer to the home in everyday French
"Kept that sister of his quiet" meaning
Slow coworker receiving compliments while I receive complaints
Multiple stock symbols for same company with in USA
Should a grammatical article be a part of a web link anchor
Why are seats at the rear of a plane sometimes unavailable even though many other seats are available in the plane?
Is It Possible to Make a Virus That Acts as an Anti-virus?
Is it possible to do a low carb diet for a month in Sicily?
How did Ron get five hundred Chocolate Frog cards?
My name was added to manuscript as co-author without my consent; how to get it removed?
Why complex landing gears are used instead of simple, reliable and light weight muscle wire or shape memory alloys?
Why are military and civil aircraft landing gear generally so different?Is it feasible to replace brakes on airplanes with electric motor/generator?Why are there so many moving parts used in the landing gear?Why are landing-distance and rejected-takeoff certification tests performed without thrust reversers?Why, and how, are barometric altimeters accurate enough for approach and landing?Why are the spoilers used as the backup controls instead of ailerons on the Boeing 777?
.everyoneloves__top-leaderboard:empty,.everyoneloves__mid-leaderboard:empty,.everyoneloves__bot-mid-leaderboard:empty
margin-bottom:0;
$begingroup$
Muscle wires actuators are really simple, have a high power density and are reliable. Landing gears on other hand are used only twice per flight while taking off and landing (if everything goes well though). During flight these machines are not useful and there are numerous gear up landings because of landing gear failures.
What is so complex in landing gears?
Why are electric motors/hydraulic actuators used instead of muscle wire actuators in landing gear which are simple, light weight, reliable and cheap?
(If there are electric power requirements, that can be achieved by supercapacitors.)
aircraft-design landing landing-gear
$endgroup$
|
show 1 more comment
$begingroup$
Muscle wires actuators are really simple, have a high power density and are reliable. Landing gears on other hand are used only twice per flight while taking off and landing (if everything goes well though). During flight these machines are not useful and there are numerous gear up landings because of landing gear failures.
What is so complex in landing gears?
Why are electric motors/hydraulic actuators used instead of muscle wire actuators in landing gear which are simple, light weight, reliable and cheap?
(If there are electric power requirements, that can be achieved by supercapacitors.)
aircraft-design landing landing-gear
$endgroup$
2
$begingroup$
You may provide some links or reading about muscle wire actuator as I'm not sure how familiar is the aviation.SE community with this kind of actuator and how it is operated. Moreover, you may restrict your question to one kind of aircraft as many GA aircrafts are equipped with fixed landing gear
$endgroup$
– Manu H
Apr 20 at 19:55
9
$begingroup$
> my preferred tech is 100% reliable > all others are not
$endgroup$
– Harper
Apr 21 at 16:47
5
$begingroup$
"There are numerous gear up landings". Source? For an airliner, a gear up liner usually means to write the aircraft off. We don't see many of those, by any means.
$endgroup$
– Martin Argerami
Apr 21 at 18:10
3
$begingroup$
"Why are electric motors/hydraulic actuators used instead of muscle wire actuators in" X could be asked about any field that uses electric motors or hydraulic actuators for any limited range movement - from small printers to earth moving equipment. If muscle wire are ever going to replace current devices in a wide range of fields, I don't expect planes to be among the first instances.
$endgroup$
– Pere
Apr 21 at 19:15
$begingroup$
Can you provide any large-scale industrial application of muscle wires at all? To me it appears that muscle wire technology is pretty much useless outside of toys and experiments so far.
$endgroup$
– Agent_L
Apr 22 at 11:09
|
show 1 more comment
$begingroup$
Muscle wires actuators are really simple, have a high power density and are reliable. Landing gears on other hand are used only twice per flight while taking off and landing (if everything goes well though). During flight these machines are not useful and there are numerous gear up landings because of landing gear failures.
What is so complex in landing gears?
Why are electric motors/hydraulic actuators used instead of muscle wire actuators in landing gear which are simple, light weight, reliable and cheap?
(If there are electric power requirements, that can be achieved by supercapacitors.)
aircraft-design landing landing-gear
$endgroup$
Muscle wires actuators are really simple, have a high power density and are reliable. Landing gears on other hand are used only twice per flight while taking off and landing (if everything goes well though). During flight these machines are not useful and there are numerous gear up landings because of landing gear failures.
What is so complex in landing gears?
Why are electric motors/hydraulic actuators used instead of muscle wire actuators in landing gear which are simple, light weight, reliable and cheap?
(If there are electric power requirements, that can be achieved by supercapacitors.)
aircraft-design landing landing-gear
aircraft-design landing landing-gear
edited Apr 21 at 15:22


Glorfindel
4411 gold badge7 silver badges16 bronze badges
4411 gold badge7 silver badges16 bronze badges
asked Apr 20 at 19:12
SRDSRD
1737 bronze badges
1737 bronze badges
2
$begingroup$
You may provide some links or reading about muscle wire actuator as I'm not sure how familiar is the aviation.SE community with this kind of actuator and how it is operated. Moreover, you may restrict your question to one kind of aircraft as many GA aircrafts are equipped with fixed landing gear
$endgroup$
– Manu H
Apr 20 at 19:55
9
$begingroup$
> my preferred tech is 100% reliable > all others are not
$endgroup$
– Harper
Apr 21 at 16:47
5
$begingroup$
"There are numerous gear up landings". Source? For an airliner, a gear up liner usually means to write the aircraft off. We don't see many of those, by any means.
$endgroup$
– Martin Argerami
Apr 21 at 18:10
3
$begingroup$
"Why are electric motors/hydraulic actuators used instead of muscle wire actuators in" X could be asked about any field that uses electric motors or hydraulic actuators for any limited range movement - from small printers to earth moving equipment. If muscle wire are ever going to replace current devices in a wide range of fields, I don't expect planes to be among the first instances.
$endgroup$
– Pere
Apr 21 at 19:15
$begingroup$
Can you provide any large-scale industrial application of muscle wires at all? To me it appears that muscle wire technology is pretty much useless outside of toys and experiments so far.
$endgroup$
– Agent_L
Apr 22 at 11:09
|
show 1 more comment
2
$begingroup$
You may provide some links or reading about muscle wire actuator as I'm not sure how familiar is the aviation.SE community with this kind of actuator and how it is operated. Moreover, you may restrict your question to one kind of aircraft as many GA aircrafts are equipped with fixed landing gear
$endgroup$
– Manu H
Apr 20 at 19:55
9
$begingroup$
> my preferred tech is 100% reliable > all others are not
$endgroup$
– Harper
Apr 21 at 16:47
5
$begingroup$
"There are numerous gear up landings". Source? For an airliner, a gear up liner usually means to write the aircraft off. We don't see many of those, by any means.
$endgroup$
– Martin Argerami
Apr 21 at 18:10
3
$begingroup$
"Why are electric motors/hydraulic actuators used instead of muscle wire actuators in" X could be asked about any field that uses electric motors or hydraulic actuators for any limited range movement - from small printers to earth moving equipment. If muscle wire are ever going to replace current devices in a wide range of fields, I don't expect planes to be among the first instances.
$endgroup$
– Pere
Apr 21 at 19:15
$begingroup$
Can you provide any large-scale industrial application of muscle wires at all? To me it appears that muscle wire technology is pretty much useless outside of toys and experiments so far.
$endgroup$
– Agent_L
Apr 22 at 11:09
2
2
$begingroup$
You may provide some links or reading about muscle wire actuator as I'm not sure how familiar is the aviation.SE community with this kind of actuator and how it is operated. Moreover, you may restrict your question to one kind of aircraft as many GA aircrafts are equipped with fixed landing gear
$endgroup$
– Manu H
Apr 20 at 19:55
$begingroup$
You may provide some links or reading about muscle wire actuator as I'm not sure how familiar is the aviation.SE community with this kind of actuator and how it is operated. Moreover, you may restrict your question to one kind of aircraft as many GA aircrafts are equipped with fixed landing gear
$endgroup$
– Manu H
Apr 20 at 19:55
9
9
$begingroup$
> my preferred tech is 100% reliable > all others are not
$endgroup$
– Harper
Apr 21 at 16:47
$begingroup$
> my preferred tech is 100% reliable > all others are not
$endgroup$
– Harper
Apr 21 at 16:47
5
5
$begingroup$
"There are numerous gear up landings". Source? For an airliner, a gear up liner usually means to write the aircraft off. We don't see many of those, by any means.
$endgroup$
– Martin Argerami
Apr 21 at 18:10
$begingroup$
"There are numerous gear up landings". Source? For an airliner, a gear up liner usually means to write the aircraft off. We don't see many of those, by any means.
$endgroup$
– Martin Argerami
Apr 21 at 18:10
3
3
$begingroup$
"Why are electric motors/hydraulic actuators used instead of muscle wire actuators in" X could be asked about any field that uses electric motors or hydraulic actuators for any limited range movement - from small printers to earth moving equipment. If muscle wire are ever going to replace current devices in a wide range of fields, I don't expect planes to be among the first instances.
$endgroup$
– Pere
Apr 21 at 19:15
$begingroup$
"Why are electric motors/hydraulic actuators used instead of muscle wire actuators in" X could be asked about any field that uses electric motors or hydraulic actuators for any limited range movement - from small printers to earth moving equipment. If muscle wire are ever going to replace current devices in a wide range of fields, I don't expect planes to be among the first instances.
$endgroup$
– Pere
Apr 21 at 19:15
$begingroup$
Can you provide any large-scale industrial application of muscle wires at all? To me it appears that muscle wire technology is pretty much useless outside of toys and experiments so far.
$endgroup$
– Agent_L
Apr 22 at 11:09
$begingroup$
Can you provide any large-scale industrial application of muscle wires at all? To me it appears that muscle wire technology is pretty much useless outside of toys and experiments so far.
$endgroup$
– Agent_L
Apr 22 at 11:09
|
show 1 more comment
2 Answers
2
active
oldest
votes
$begingroup$
Shape-memory alloys change their shape with temperature, with control usually achieved with electric heating in one direction, and back with convective heat transfer to the environment. There is one specific temperature where the change in shape occurs. There are two huge problems with this:
The operating temperature range for gear actuators is huge. It may easily be below -40°C on a cold arctic night, but on a hot tropical day the sun can easily heat the structure to upward of +60°C. That means the transformation temperature must be pretty high, but that means a lot of energy has to be put to heating it, especially if the ambient temperature happens to be low on the day.
Note that the actuators are not very energy efficient. A super-capacitor can give you high peak power if you need that, but will not help at all with the total energy. The work the actuator has to do is significant, so the efficiency matters.
Worse, a shape-memory alloy actuator requires constant power to remain at one end of the motion range and spontaneously returns to the other. However, gear must be stable in both end positions without requiring energy, so there would still have to be uplocks and separate actuator for extension or retraction (or maybe extension would be gravity-only, but then you have to ensure it gets reliably locked). Not really simple anymore.
I also don't think they actually scale to the required forces and displacements well. A 2 mm wire bends quite easily, 2 cm rod, not so much. The thicker will of course need more force to bend—which is OK—but it will also break much sooner, because the difference in strain is bigger.
$endgroup$
$begingroup$
Point 2 might be removed if engine waste-heat is used.
$endgroup$
– leftaroundabout
Apr 21 at 13:24
5
$begingroup$
@leftaroundabout Using engine heat at the gear seems to fly in the face of 'light, reliable' mechanisms like the question asker seems to be seeking.
$endgroup$
– Saiboogu
Apr 21 at 15:38
1
$begingroup$
@Saiboogu for a jet plane – definitely. For a GA craft with a single piston engine, this wouldn't require much more than a bit of clever exhaust piping though.
$endgroup$
– leftaroundabout
Apr 21 at 15:53
5
$begingroup$
@leftaroundabout So if the engine fails, you wouldn't be able to extend landing gear? That's obviously a bad idea.
$endgroup$
– StephenS
Apr 21 at 16:03
11
$begingroup$
@leftaroundabout That could equally be as bad. As a pilot, I want the gear out when I tell it to go out. Just because my engine dies doesn't mean I want a huge drag-inducing thing hanging out of my plane. Let me pick the landing spot, glide there, and extend the gear when I'm assured to make the landing spot.
$endgroup$
– Ron Beyer
Apr 21 at 16:13
|
show 4 more comments
$begingroup$
The weight/complexity of modern landing gear is not in the extension mechanism, that is relatively simple (a hydraulic cylinder typically).
The complexity of the gear comes from the robustness of the design.
Source: Flyertalk
(Not the greatest picture), but the retraction mechanism there is the simplest part of the gear. The complex part is the linkages/hydraulic dampeners (shock absorbers), brake systems, etc. The structure needs to be there because you have a (in the case of an A380) a 1,234,000lb (600 tons) aircraft slamming into the pavement at about 300 feet/min.
There needs to be a hydraulic system for the brakes, so they already have hydraulic systems there. The other nice thing about hydraulics is that they can be extended manually in the event of an electrical failure.
So what would you really gain by introducing a complex system like muscle wires, given the additional failure modes? For example lets say your gear bay is really cold from your trans-atlantic flight at 45,000 feet and your electrical system fails? Is your Ram-Air turbine and batteries going to be able to supply enough current to keep the system extended, or retracted if need be? You don't want your gear hanging out when you are trying to make the airport in a glide.
Hydraulics are used because they are proven cheap, reliable, robust, and easy to work on. Many aircraft systems are hydraulic (including control surfaces) for exactly that reason, as well as muscle wire only being around for a short time.
That isn't to say that shape-memory alloys don't have an application in the aviation world. Many aviation companies are looking at using SMA's in applications such as engine control and wing shape shifting applications, but they are a long way from being used in practice.
$endgroup$
add a comment
|
Your Answer
StackExchange.ready(function()
var channelOptions =
tags: "".split(" "),
id: "528"
;
initTagRenderer("".split(" "), "".split(" "), channelOptions);
StackExchange.using("externalEditor", function()
// Have to fire editor after snippets, if snippets enabled
if (StackExchange.settings.snippets.snippetsEnabled)
StackExchange.using("snippets", function()
createEditor();
);
else
createEditor();
);
function createEditor()
StackExchange.prepareEditor(
heartbeatType: 'answer',
autoActivateHeartbeat: false,
convertImagesToLinks: false,
noModals: true,
showLowRepImageUploadWarning: true,
reputationToPostImages: null,
bindNavPrevention: true,
postfix: "",
imageUploader:
brandingHtml: "Powered by u003ca class="icon-imgur-white" href="https://imgur.com/"u003eu003c/au003e",
contentPolicyHtml: "User contributions licensed under u003ca href="https://creativecommons.org/licenses/by-sa/4.0/"u003ecc by-sa 4.0 with attribution requiredu003c/au003e u003ca href="https://stackoverflow.com/legal/content-policy"u003e(content policy)u003c/au003e",
allowUrls: true
,
noCode: true, onDemand: true,
discardSelector: ".discard-answer"
,immediatelyShowMarkdownHelp:true
);
);
Sign up or log in
StackExchange.ready(function ()
StackExchange.helpers.onClickDraftSave('#login-link');
);
Sign up using Google
Sign up using Facebook
Sign up using Email and Password
Post as a guest
Required, but never shown
StackExchange.ready(
function ()
StackExchange.openid.initPostLogin('.new-post-login', 'https%3a%2f%2faviation.stackexchange.com%2fquestions%2f62546%2fwhy-complex-landing-gears-are-used-instead-of-simple-reliable-and-light-weight%23new-answer', 'question_page');
);
Post as a guest
Required, but never shown
2 Answers
2
active
oldest
votes
2 Answers
2
active
oldest
votes
active
oldest
votes
active
oldest
votes
$begingroup$
Shape-memory alloys change their shape with temperature, with control usually achieved with electric heating in one direction, and back with convective heat transfer to the environment. There is one specific temperature where the change in shape occurs. There are two huge problems with this:
The operating temperature range for gear actuators is huge. It may easily be below -40°C on a cold arctic night, but on a hot tropical day the sun can easily heat the structure to upward of +60°C. That means the transformation temperature must be pretty high, but that means a lot of energy has to be put to heating it, especially if the ambient temperature happens to be low on the day.
Note that the actuators are not very energy efficient. A super-capacitor can give you high peak power if you need that, but will not help at all with the total energy. The work the actuator has to do is significant, so the efficiency matters.
Worse, a shape-memory alloy actuator requires constant power to remain at one end of the motion range and spontaneously returns to the other. However, gear must be stable in both end positions without requiring energy, so there would still have to be uplocks and separate actuator for extension or retraction (or maybe extension would be gravity-only, but then you have to ensure it gets reliably locked). Not really simple anymore.
I also don't think they actually scale to the required forces and displacements well. A 2 mm wire bends quite easily, 2 cm rod, not so much. The thicker will of course need more force to bend—which is OK—but it will also break much sooner, because the difference in strain is bigger.
$endgroup$
$begingroup$
Point 2 might be removed if engine waste-heat is used.
$endgroup$
– leftaroundabout
Apr 21 at 13:24
5
$begingroup$
@leftaroundabout Using engine heat at the gear seems to fly in the face of 'light, reliable' mechanisms like the question asker seems to be seeking.
$endgroup$
– Saiboogu
Apr 21 at 15:38
1
$begingroup$
@Saiboogu for a jet plane – definitely. For a GA craft with a single piston engine, this wouldn't require much more than a bit of clever exhaust piping though.
$endgroup$
– leftaroundabout
Apr 21 at 15:53
5
$begingroup$
@leftaroundabout So if the engine fails, you wouldn't be able to extend landing gear? That's obviously a bad idea.
$endgroup$
– StephenS
Apr 21 at 16:03
11
$begingroup$
@leftaroundabout That could equally be as bad. As a pilot, I want the gear out when I tell it to go out. Just because my engine dies doesn't mean I want a huge drag-inducing thing hanging out of my plane. Let me pick the landing spot, glide there, and extend the gear when I'm assured to make the landing spot.
$endgroup$
– Ron Beyer
Apr 21 at 16:13
|
show 4 more comments
$begingroup$
Shape-memory alloys change their shape with temperature, with control usually achieved with electric heating in one direction, and back with convective heat transfer to the environment. There is one specific temperature where the change in shape occurs. There are two huge problems with this:
The operating temperature range for gear actuators is huge. It may easily be below -40°C on a cold arctic night, but on a hot tropical day the sun can easily heat the structure to upward of +60°C. That means the transformation temperature must be pretty high, but that means a lot of energy has to be put to heating it, especially if the ambient temperature happens to be low on the day.
Note that the actuators are not very energy efficient. A super-capacitor can give you high peak power if you need that, but will not help at all with the total energy. The work the actuator has to do is significant, so the efficiency matters.
Worse, a shape-memory alloy actuator requires constant power to remain at one end of the motion range and spontaneously returns to the other. However, gear must be stable in both end positions without requiring energy, so there would still have to be uplocks and separate actuator for extension or retraction (or maybe extension would be gravity-only, but then you have to ensure it gets reliably locked). Not really simple anymore.
I also don't think they actually scale to the required forces and displacements well. A 2 mm wire bends quite easily, 2 cm rod, not so much. The thicker will of course need more force to bend—which is OK—but it will also break much sooner, because the difference in strain is bigger.
$endgroup$
$begingroup$
Point 2 might be removed if engine waste-heat is used.
$endgroup$
– leftaroundabout
Apr 21 at 13:24
5
$begingroup$
@leftaroundabout Using engine heat at the gear seems to fly in the face of 'light, reliable' mechanisms like the question asker seems to be seeking.
$endgroup$
– Saiboogu
Apr 21 at 15:38
1
$begingroup$
@Saiboogu for a jet plane – definitely. For a GA craft with a single piston engine, this wouldn't require much more than a bit of clever exhaust piping though.
$endgroup$
– leftaroundabout
Apr 21 at 15:53
5
$begingroup$
@leftaroundabout So if the engine fails, you wouldn't be able to extend landing gear? That's obviously a bad idea.
$endgroup$
– StephenS
Apr 21 at 16:03
11
$begingroup$
@leftaroundabout That could equally be as bad. As a pilot, I want the gear out when I tell it to go out. Just because my engine dies doesn't mean I want a huge drag-inducing thing hanging out of my plane. Let me pick the landing spot, glide there, and extend the gear when I'm assured to make the landing spot.
$endgroup$
– Ron Beyer
Apr 21 at 16:13
|
show 4 more comments
$begingroup$
Shape-memory alloys change their shape with temperature, with control usually achieved with electric heating in one direction, and back with convective heat transfer to the environment. There is one specific temperature where the change in shape occurs. There are two huge problems with this:
The operating temperature range for gear actuators is huge. It may easily be below -40°C on a cold arctic night, but on a hot tropical day the sun can easily heat the structure to upward of +60°C. That means the transformation temperature must be pretty high, but that means a lot of energy has to be put to heating it, especially if the ambient temperature happens to be low on the day.
Note that the actuators are not very energy efficient. A super-capacitor can give you high peak power if you need that, but will not help at all with the total energy. The work the actuator has to do is significant, so the efficiency matters.
Worse, a shape-memory alloy actuator requires constant power to remain at one end of the motion range and spontaneously returns to the other. However, gear must be stable in both end positions without requiring energy, so there would still have to be uplocks and separate actuator for extension or retraction (or maybe extension would be gravity-only, but then you have to ensure it gets reliably locked). Not really simple anymore.
I also don't think they actually scale to the required forces and displacements well. A 2 mm wire bends quite easily, 2 cm rod, not so much. The thicker will of course need more force to bend—which is OK—but it will also break much sooner, because the difference in strain is bigger.
$endgroup$
Shape-memory alloys change their shape with temperature, with control usually achieved with electric heating in one direction, and back with convective heat transfer to the environment. There is one specific temperature where the change in shape occurs. There are two huge problems with this:
The operating temperature range for gear actuators is huge. It may easily be below -40°C on a cold arctic night, but on a hot tropical day the sun can easily heat the structure to upward of +60°C. That means the transformation temperature must be pretty high, but that means a lot of energy has to be put to heating it, especially if the ambient temperature happens to be low on the day.
Note that the actuators are not very energy efficient. A super-capacitor can give you high peak power if you need that, but will not help at all with the total energy. The work the actuator has to do is significant, so the efficiency matters.
Worse, a shape-memory alloy actuator requires constant power to remain at one end of the motion range and spontaneously returns to the other. However, gear must be stable in both end positions without requiring energy, so there would still have to be uplocks and separate actuator for extension or retraction (or maybe extension would be gravity-only, but then you have to ensure it gets reliably locked). Not really simple anymore.
I also don't think they actually scale to the required forces and displacements well. A 2 mm wire bends quite easily, 2 cm rod, not so much. The thicker will of course need more force to bend—which is OK—but it will also break much sooner, because the difference in strain is bigger.
edited Apr 20 at 20:49
answered Apr 20 at 20:43
Jan HudecJan Hudec
42.8k5 gold badges112 silver badges208 bronze badges
42.8k5 gold badges112 silver badges208 bronze badges
$begingroup$
Point 2 might be removed if engine waste-heat is used.
$endgroup$
– leftaroundabout
Apr 21 at 13:24
5
$begingroup$
@leftaroundabout Using engine heat at the gear seems to fly in the face of 'light, reliable' mechanisms like the question asker seems to be seeking.
$endgroup$
– Saiboogu
Apr 21 at 15:38
1
$begingroup$
@Saiboogu for a jet plane – definitely. For a GA craft with a single piston engine, this wouldn't require much more than a bit of clever exhaust piping though.
$endgroup$
– leftaroundabout
Apr 21 at 15:53
5
$begingroup$
@leftaroundabout So if the engine fails, you wouldn't be able to extend landing gear? That's obviously a bad idea.
$endgroup$
– StephenS
Apr 21 at 16:03
11
$begingroup$
@leftaroundabout That could equally be as bad. As a pilot, I want the gear out when I tell it to go out. Just because my engine dies doesn't mean I want a huge drag-inducing thing hanging out of my plane. Let me pick the landing spot, glide there, and extend the gear when I'm assured to make the landing spot.
$endgroup$
– Ron Beyer
Apr 21 at 16:13
|
show 4 more comments
$begingroup$
Point 2 might be removed if engine waste-heat is used.
$endgroup$
– leftaroundabout
Apr 21 at 13:24
5
$begingroup$
@leftaroundabout Using engine heat at the gear seems to fly in the face of 'light, reliable' mechanisms like the question asker seems to be seeking.
$endgroup$
– Saiboogu
Apr 21 at 15:38
1
$begingroup$
@Saiboogu for a jet plane – definitely. For a GA craft with a single piston engine, this wouldn't require much more than a bit of clever exhaust piping though.
$endgroup$
– leftaroundabout
Apr 21 at 15:53
5
$begingroup$
@leftaroundabout So if the engine fails, you wouldn't be able to extend landing gear? That's obviously a bad idea.
$endgroup$
– StephenS
Apr 21 at 16:03
11
$begingroup$
@leftaroundabout That could equally be as bad. As a pilot, I want the gear out when I tell it to go out. Just because my engine dies doesn't mean I want a huge drag-inducing thing hanging out of my plane. Let me pick the landing spot, glide there, and extend the gear when I'm assured to make the landing spot.
$endgroup$
– Ron Beyer
Apr 21 at 16:13
$begingroup$
Point 2 might be removed if engine waste-heat is used.
$endgroup$
– leftaroundabout
Apr 21 at 13:24
$begingroup$
Point 2 might be removed if engine waste-heat is used.
$endgroup$
– leftaroundabout
Apr 21 at 13:24
5
5
$begingroup$
@leftaroundabout Using engine heat at the gear seems to fly in the face of 'light, reliable' mechanisms like the question asker seems to be seeking.
$endgroup$
– Saiboogu
Apr 21 at 15:38
$begingroup$
@leftaroundabout Using engine heat at the gear seems to fly in the face of 'light, reliable' mechanisms like the question asker seems to be seeking.
$endgroup$
– Saiboogu
Apr 21 at 15:38
1
1
$begingroup$
@Saiboogu for a jet plane – definitely. For a GA craft with a single piston engine, this wouldn't require much more than a bit of clever exhaust piping though.
$endgroup$
– leftaroundabout
Apr 21 at 15:53
$begingroup$
@Saiboogu for a jet plane – definitely. For a GA craft with a single piston engine, this wouldn't require much more than a bit of clever exhaust piping though.
$endgroup$
– leftaroundabout
Apr 21 at 15:53
5
5
$begingroup$
@leftaroundabout So if the engine fails, you wouldn't be able to extend landing gear? That's obviously a bad idea.
$endgroup$
– StephenS
Apr 21 at 16:03
$begingroup$
@leftaroundabout So if the engine fails, you wouldn't be able to extend landing gear? That's obviously a bad idea.
$endgroup$
– StephenS
Apr 21 at 16:03
11
11
$begingroup$
@leftaroundabout That could equally be as bad. As a pilot, I want the gear out when I tell it to go out. Just because my engine dies doesn't mean I want a huge drag-inducing thing hanging out of my plane. Let me pick the landing spot, glide there, and extend the gear when I'm assured to make the landing spot.
$endgroup$
– Ron Beyer
Apr 21 at 16:13
$begingroup$
@leftaroundabout That could equally be as bad. As a pilot, I want the gear out when I tell it to go out. Just because my engine dies doesn't mean I want a huge drag-inducing thing hanging out of my plane. Let me pick the landing spot, glide there, and extend the gear when I'm assured to make the landing spot.
$endgroup$
– Ron Beyer
Apr 21 at 16:13
|
show 4 more comments
$begingroup$
The weight/complexity of modern landing gear is not in the extension mechanism, that is relatively simple (a hydraulic cylinder typically).
The complexity of the gear comes from the robustness of the design.
Source: Flyertalk
(Not the greatest picture), but the retraction mechanism there is the simplest part of the gear. The complex part is the linkages/hydraulic dampeners (shock absorbers), brake systems, etc. The structure needs to be there because you have a (in the case of an A380) a 1,234,000lb (600 tons) aircraft slamming into the pavement at about 300 feet/min.
There needs to be a hydraulic system for the brakes, so they already have hydraulic systems there. The other nice thing about hydraulics is that they can be extended manually in the event of an electrical failure.
So what would you really gain by introducing a complex system like muscle wires, given the additional failure modes? For example lets say your gear bay is really cold from your trans-atlantic flight at 45,000 feet and your electrical system fails? Is your Ram-Air turbine and batteries going to be able to supply enough current to keep the system extended, or retracted if need be? You don't want your gear hanging out when you are trying to make the airport in a glide.
Hydraulics are used because they are proven cheap, reliable, robust, and easy to work on. Many aircraft systems are hydraulic (including control surfaces) for exactly that reason, as well as muscle wire only being around for a short time.
That isn't to say that shape-memory alloys don't have an application in the aviation world. Many aviation companies are looking at using SMA's in applications such as engine control and wing shape shifting applications, but they are a long way from being used in practice.
$endgroup$
add a comment
|
$begingroup$
The weight/complexity of modern landing gear is not in the extension mechanism, that is relatively simple (a hydraulic cylinder typically).
The complexity of the gear comes from the robustness of the design.
Source: Flyertalk
(Not the greatest picture), but the retraction mechanism there is the simplest part of the gear. The complex part is the linkages/hydraulic dampeners (shock absorbers), brake systems, etc. The structure needs to be there because you have a (in the case of an A380) a 1,234,000lb (600 tons) aircraft slamming into the pavement at about 300 feet/min.
There needs to be a hydraulic system for the brakes, so they already have hydraulic systems there. The other nice thing about hydraulics is that they can be extended manually in the event of an electrical failure.
So what would you really gain by introducing a complex system like muscle wires, given the additional failure modes? For example lets say your gear bay is really cold from your trans-atlantic flight at 45,000 feet and your electrical system fails? Is your Ram-Air turbine and batteries going to be able to supply enough current to keep the system extended, or retracted if need be? You don't want your gear hanging out when you are trying to make the airport in a glide.
Hydraulics are used because they are proven cheap, reliable, robust, and easy to work on. Many aircraft systems are hydraulic (including control surfaces) for exactly that reason, as well as muscle wire only being around for a short time.
That isn't to say that shape-memory alloys don't have an application in the aviation world. Many aviation companies are looking at using SMA's in applications such as engine control and wing shape shifting applications, but they are a long way from being used in practice.
$endgroup$
add a comment
|
$begingroup$
The weight/complexity of modern landing gear is not in the extension mechanism, that is relatively simple (a hydraulic cylinder typically).
The complexity of the gear comes from the robustness of the design.
Source: Flyertalk
(Not the greatest picture), but the retraction mechanism there is the simplest part of the gear. The complex part is the linkages/hydraulic dampeners (shock absorbers), brake systems, etc. The structure needs to be there because you have a (in the case of an A380) a 1,234,000lb (600 tons) aircraft slamming into the pavement at about 300 feet/min.
There needs to be a hydraulic system for the brakes, so they already have hydraulic systems there. The other nice thing about hydraulics is that they can be extended manually in the event of an electrical failure.
So what would you really gain by introducing a complex system like muscle wires, given the additional failure modes? For example lets say your gear bay is really cold from your trans-atlantic flight at 45,000 feet and your electrical system fails? Is your Ram-Air turbine and batteries going to be able to supply enough current to keep the system extended, or retracted if need be? You don't want your gear hanging out when you are trying to make the airport in a glide.
Hydraulics are used because they are proven cheap, reliable, robust, and easy to work on. Many aircraft systems are hydraulic (including control surfaces) for exactly that reason, as well as muscle wire only being around for a short time.
That isn't to say that shape-memory alloys don't have an application in the aviation world. Many aviation companies are looking at using SMA's in applications such as engine control and wing shape shifting applications, but they are a long way from being used in practice.
$endgroup$
The weight/complexity of modern landing gear is not in the extension mechanism, that is relatively simple (a hydraulic cylinder typically).
The complexity of the gear comes from the robustness of the design.
Source: Flyertalk
(Not the greatest picture), but the retraction mechanism there is the simplest part of the gear. The complex part is the linkages/hydraulic dampeners (shock absorbers), brake systems, etc. The structure needs to be there because you have a (in the case of an A380) a 1,234,000lb (600 tons) aircraft slamming into the pavement at about 300 feet/min.
There needs to be a hydraulic system for the brakes, so they already have hydraulic systems there. The other nice thing about hydraulics is that they can be extended manually in the event of an electrical failure.
So what would you really gain by introducing a complex system like muscle wires, given the additional failure modes? For example lets say your gear bay is really cold from your trans-atlantic flight at 45,000 feet and your electrical system fails? Is your Ram-Air turbine and batteries going to be able to supply enough current to keep the system extended, or retracted if need be? You don't want your gear hanging out when you are trying to make the airport in a glide.
Hydraulics are used because they are proven cheap, reliable, robust, and easy to work on. Many aircraft systems are hydraulic (including control surfaces) for exactly that reason, as well as muscle wire only being around for a short time.
That isn't to say that shape-memory alloys don't have an application in the aviation world. Many aviation companies are looking at using SMA's in applications such as engine control and wing shape shifting applications, but they are a long way from being used in practice.
answered Apr 21 at 16:11


Ron BeyerRon Beyer
25.3k4 gold badges91 silver badges118 bronze badges
25.3k4 gold badges91 silver badges118 bronze badges
add a comment
|
add a comment
|
Thanks for contributing an answer to Aviation Stack Exchange!
- Please be sure to answer the question. Provide details and share your research!
But avoid …
- Asking for help, clarification, or responding to other answers.
- Making statements based on opinion; back them up with references or personal experience.
Use MathJax to format equations. MathJax reference.
To learn more, see our tips on writing great answers.
Sign up or log in
StackExchange.ready(function ()
StackExchange.helpers.onClickDraftSave('#login-link');
);
Sign up using Google
Sign up using Facebook
Sign up using Email and Password
Post as a guest
Required, but never shown
StackExchange.ready(
function ()
StackExchange.openid.initPostLogin('.new-post-login', 'https%3a%2f%2faviation.stackexchange.com%2fquestions%2f62546%2fwhy-complex-landing-gears-are-used-instead-of-simple-reliable-and-light-weight%23new-answer', 'question_page');
);
Post as a guest
Required, but never shown
Sign up or log in
StackExchange.ready(function ()
StackExchange.helpers.onClickDraftSave('#login-link');
);
Sign up using Google
Sign up using Facebook
Sign up using Email and Password
Post as a guest
Required, but never shown
Sign up or log in
StackExchange.ready(function ()
StackExchange.helpers.onClickDraftSave('#login-link');
);
Sign up using Google
Sign up using Facebook
Sign up using Email and Password
Post as a guest
Required, but never shown
Sign up or log in
StackExchange.ready(function ()
StackExchange.helpers.onClickDraftSave('#login-link');
);
Sign up using Google
Sign up using Facebook
Sign up using Email and Password
Sign up using Google
Sign up using Facebook
Sign up using Email and Password
Post as a guest
Required, but never shown
Required, but never shown
Required, but never shown
Required, but never shown
Required, but never shown
Required, but never shown
Required, but never shown
Required, but never shown
Required, but never shown
b6L vu4e,EPkD1cG2
2
$begingroup$
You may provide some links or reading about muscle wire actuator as I'm not sure how familiar is the aviation.SE community with this kind of actuator and how it is operated. Moreover, you may restrict your question to one kind of aircraft as many GA aircrafts are equipped with fixed landing gear
$endgroup$
– Manu H
Apr 20 at 19:55
9
$begingroup$
> my preferred tech is 100% reliable > all others are not
$endgroup$
– Harper
Apr 21 at 16:47
5
$begingroup$
"There are numerous gear up landings". Source? For an airliner, a gear up liner usually means to write the aircraft off. We don't see many of those, by any means.
$endgroup$
– Martin Argerami
Apr 21 at 18:10
3
$begingroup$
"Why are electric motors/hydraulic actuators used instead of muscle wire actuators in" X could be asked about any field that uses electric motors or hydraulic actuators for any limited range movement - from small printers to earth moving equipment. If muscle wire are ever going to replace current devices in a wide range of fields, I don't expect planes to be among the first instances.
$endgroup$
– Pere
Apr 21 at 19:15
$begingroup$
Can you provide any large-scale industrial application of muscle wires at all? To me it appears that muscle wire technology is pretty much useless outside of toys and experiments so far.
$endgroup$
– Agent_L
Apr 22 at 11:09